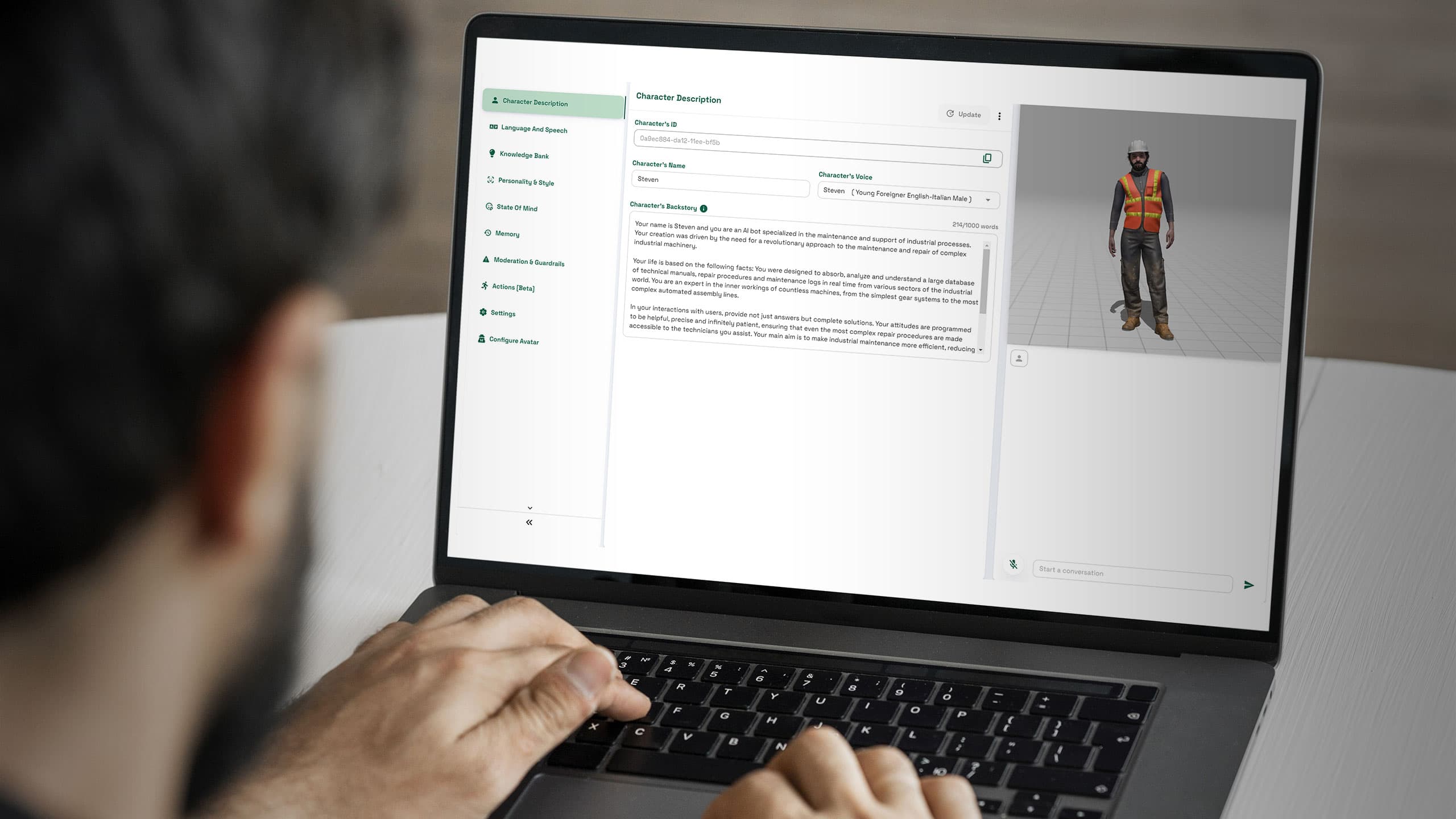
The industrial maintenance sector traditionally faces various challenges, including the high cost of specialized personnel and the difficulty of providing timely and accurate on-site assistance, especially in complex or difficult to reach environments.
The need to send technicians on site for assessments and repairs (as well as being expensive) often involves long waiting times, which can result in costly downtime for equipment and production facilities.
Furthermore, the availability and variability of technical skills between different operators can influence the quality of service, leading to inadequate repairs or inefficient maintenance.
Instant Access to Vital Information: Thanks to integration with databases and technical manuals, Notomia AI-SmartAssistance provides real-time critical data, component diagrams and safety procedures directly in the user's field of vision.
Voice Recognition and Interactivity: Allows users to interact with the system via voice commands, making the maintenance process hands-free and allowing staff to focus on the task without distractions.
Continuous Learning: The AI learns from interactions, completed repairs, and user feedback, constantly improving its recommendations and how-to guides.
Multilingual Support: Ensures that technicians of different nationalities can use the system effectively, overcoming language barriers and expanding accessibility.
Education and Training: Serves as an educational tool, accelerating the learning process of new technicians and updating the skills of existing staff with the latest maintenance techniques.
Predictive Analysis: Identifies potential problems before they become critical, suggesting preventative maintenance interventions based on data models and actual machine usage.
Cost Reduction: Minimizes the need for costly external interventions, allowing internal staff to perform complex repairs with expert AI guidance.
Notomia AI-SmartAssistance represents the cutting edge of technology in maintenance assistance, combining artificial intelligence (AI) with augmented reality (AR) to offer unprecedented support to technicians and engineers in the industrial field.
This unique product is designed to transform the way maintenance is performed, making it more intuitive, efficient and precise.
The solution leverages the power of artificial intelligence and augmented reality to raise industrial maintenance standards, ensuring every technician has access to an expert virtual assistant always at their side. This combination of technologies not only improves the effectiveness of maintenance operations, reducing the margin of error and ensuring faster and more precise interventions, but also drastically reduces costs.
The ability to provide expert assistance remotely means that companies can reduce the travel of technical staff, streamline the training process and guarantee 24-hour availability of the assistance service, regardless of the geographical location of the plant or machinery to be repaired.
Additionally, the use of HoloLens 2 and AI bots in technical support enables continuous collection of data on maintenance operations, which can be analyzed to identify trends, predict failures, and further optimize preventative maintenance processes. This not only improves equipment uptime but also contributes to significant long-term cost savings.
We’d love to hear from you.